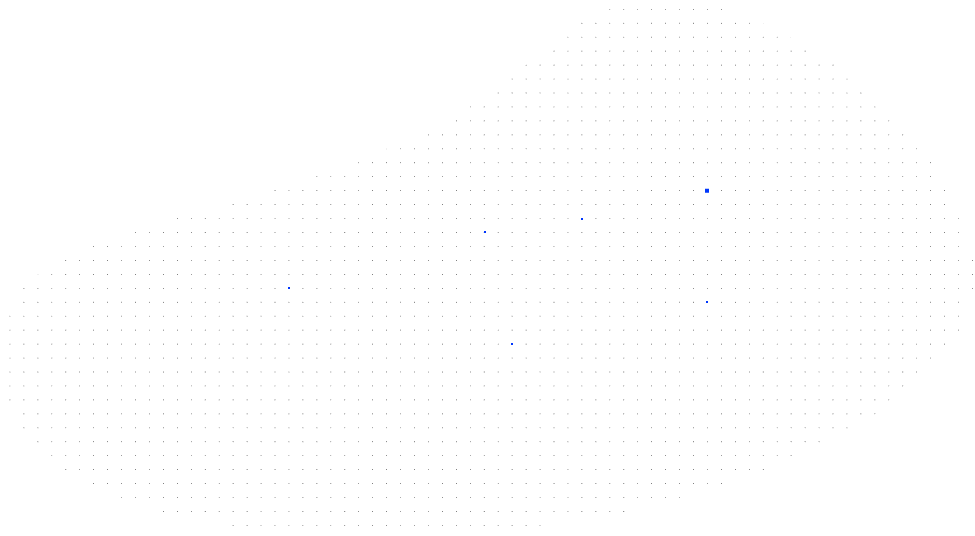
ML-Spock
Machine Learning Supported System for Performance Assessment of Steel Structures Under Extreme Operating Conditions and Management of Risk

Abstract
Building sustainable cities require action and technologies that minimize the large lifecycle costs of infrastructure assets. These costs relate to the way infrastructure responds to operating conditions and are further exacerbated by laborious visual inspections aimed at ensuring structural safety. This is relevant for steel structures, which are commonly used for community-critical infrastructure. At the center of this problem lies the quantification of reserve load-bearing capacity of structures.
With the overarching goal of minimizing downtime and managing risks of the built infrastructure, the focus of this project is on the development of enabling data-driven methods, which can assist in the reliable rapid diagnosis of damage. One of the novel concepts at the core of the envisioned methodological framework is the direct mapping of deformed structural shapes to the associated reserve capacity by relying on visual deformations. To this end, validated nonlinear constitutive material models and computational workflows developed within the PI’s group will be leveraged to generate comprehensive training data for the development of machine learning (ML) tools. A further novelty lies in the use of a common data interface based on the 3D digital objects of deformed shapes, which allows for consistent treatment of physical and numerical data. This is key for the envisioned experimental validation and streamlined application of the methodology. Moreover, we propose a novel approach, based on engineering insight, for extraction of domain-specific features from the deformed steel members, which can be directly used as inputs to available ML tools.
The theoretical developments and associated computational tools of this project can be generalized and expanded for structures made of other construction materials by developing additional modules. These modules can be encapsulated in a software ecosystem to comprehensively support automated inspection of infrastructure.
People
Collaborators
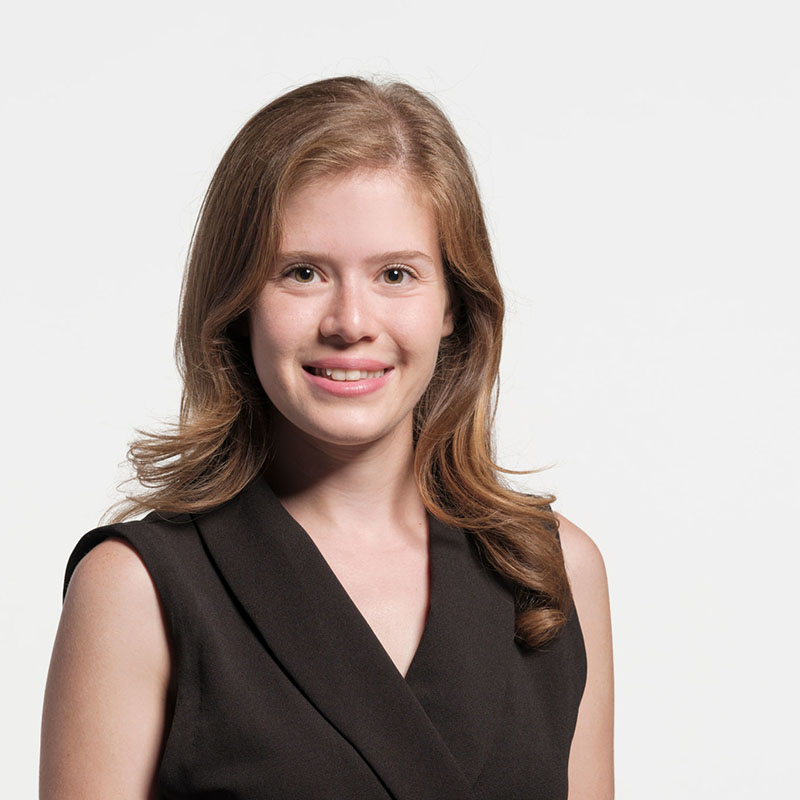
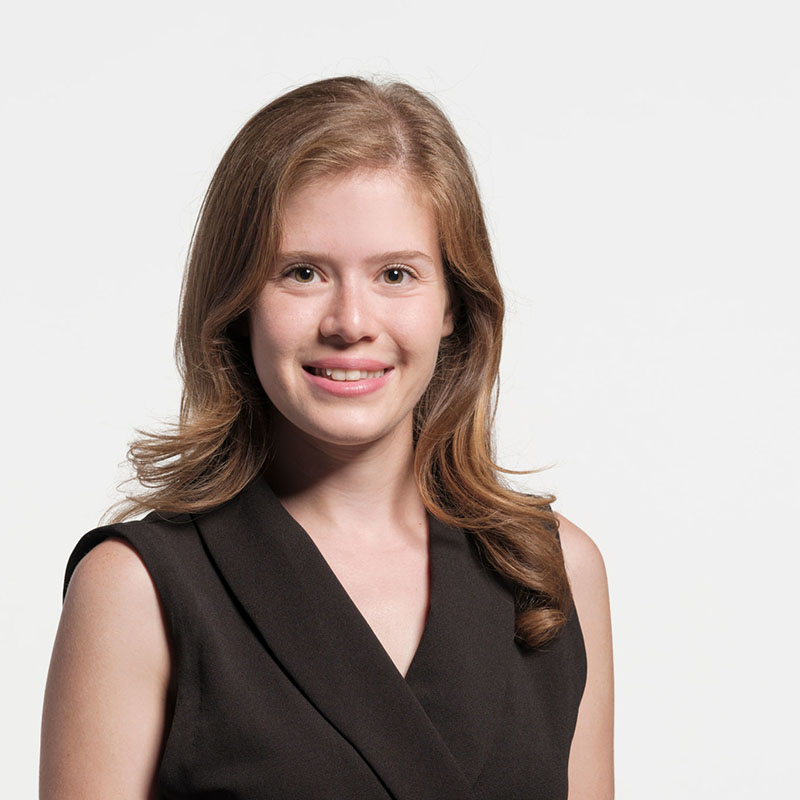
Isinsu joined the SDSC in May 2022. She obtained a Bachelor’s degree in Computer Science from Middle East Technical University, Turkey, and later received a Master’s degree in Computer Science from EPFL. She conducted her doctoral studies in the Computer Vision Lab at EPFL with a focus on human body pose estimation and motion prediction using deep learning-based methods. Her research interests include self- and semi-supervised learning for image-based analysis of the human body and motion, with applications ranging from athletic training to healthcare.
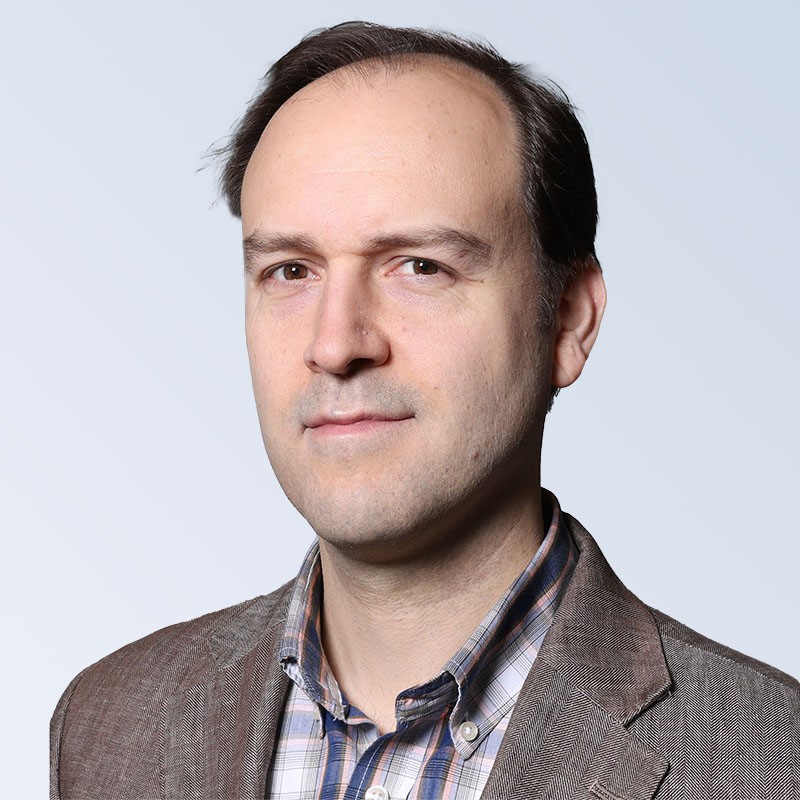
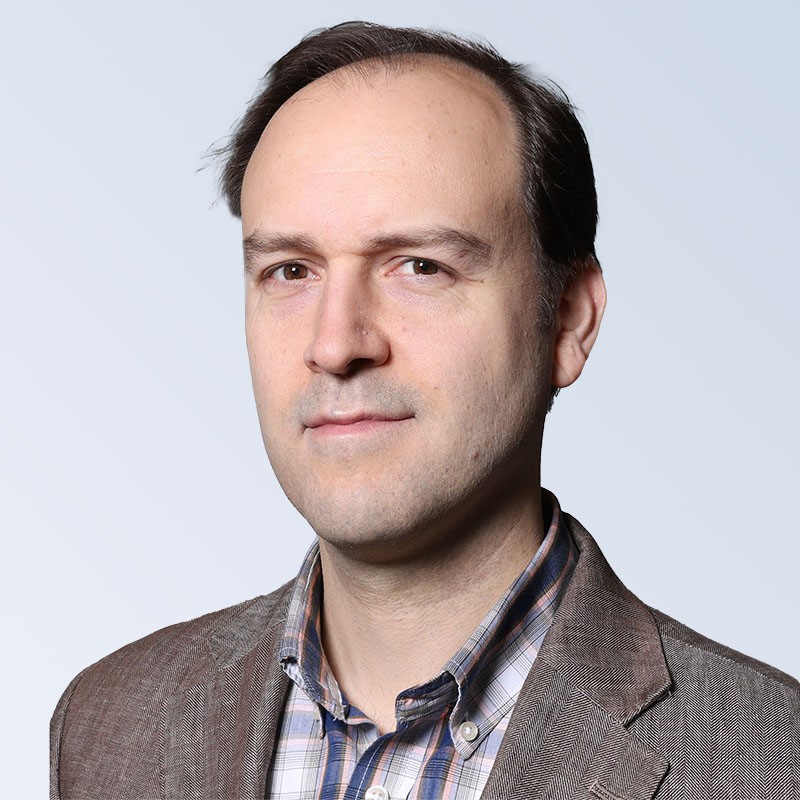
Guillaume Obozinski graduated with a PhD in Statistics from UC Berkeley in 2009. He did his postdoc and held until 2012 a researcher position in the Willow and Sierra teams at INRIA and Ecole Normale Supérieure in Paris. He was then Research Faculty at Ecole des Ponts ParisTech until 2018. Guillaume has broad interests in statistics and machine learning and worked over time on sparse modeling, optimization for large scale learning, graphical models, relational learning and semantic embeddings, with applications in various domains from computational biology to computer vision.
PI | Partners:
EPFL, Resilient Steel Structures Laboratory:
- Prof. Dimitrios Lignos
- Dr. Nenad Bijelic
- Tianyu Gu
description
Motivation
This project focuses on steel structures commonly used in building and bridge construction, renowned for their ductility. Exposure to extreme conditions such as snowstorms, heavy traffic, or earthquakes results in inelastic deformation in these structures, diminishing their residual life. Traditional condition assessments heavily depend on periodic (human) visual inspections, a process prone to unreliability and risks for inspectors. The collaborative goal is to develop a novel, data-driven methodology for automated and reliable residual life (reserve capacity) prognosis of steel members in infrastructure systems based on visual data.
Proposed Approach / Solution
In this project, we explored various machine learning algorithms that rely solely on observed 3D deformations of steel members to assess their damage state, given that loading history in realistic settings is typically unavailable. To achieve this, we investigated different representations of a 3D digital object and fed the processed 3D point cloud of the deformed shape to the underlying machine learning model, as illustrated in Figure 1. The ground truth data was generated through high-fidelity numerical simulations of steel members, with a major focus on generalizing from the experimental laboratory environment to real-world settings. The simulations captured key behavioral transitions such as buckling-induced reductions in reserve capacity, as shown in Figure 2.
Our proposed approach involved slicing the digital 3D objects into structured grids, which can be used in combination with pointwise MLP methods. Using a PointTransformer model, which applies attention within local neighborhoods around centroids in the point cloud, we demonstrated that this deep learning model can robustly estimate the reserve capacity of structural elements from their point cloud. Although including information beyond visual traces of deformation is not essential for robust quantification of the reserve capacity, incorporating the axial load ratio, member boundary conditions, and column dimensions as predictive features further reduced the error by approximately 20% to 25%. This is a practical finding given that these features can be estimated by engineers in a straightforward way if such additional accuracy is merited. Alternatively, integrating an auxiliary classification task—classifying the loading protocol, boundary condition, and loading ratio—enabled the model to learn a more discriminative feature space for point cloud embeddings, ultimately enhancing reserve capacity prediction accuracy. Given that the loading history of a structural member is typically unknown and cannot be inferred as accurately, these results highlight the primary importance of the deformed shape (rather than how the structural member came to be so deformed) on the associated reserve capacity.


Impact
This project's scientific breakthrough is quantifying the remaining lifespan of steel structures based on visual data alone. This can greatly simplify costly inspections, support expert training, and reduce reliance on time-consuming manual inspections that pose risks to humans. Moreover, the framework developed in this project can be used in drones or robots for automated inspection in hazardous environments. Finally, early damage identification enables proper remediation, making the infrastructure more sustainable and decreases its carbon footprint.
Presentation
Gallery
Annexe
Additional resources
Bibliography
- Spencer, B.F. et al (2019). Advances in Computer Vision-Based Civil Infrastructure Inspection and Monitoring. Engineering 5(2):199-222. https://www.sciencedirect.com/science/article/pii/S2095809918308130
- Elkady, A. and Lignos, D.G. (2015). Analytical investigation of the cyclic behavior and plastic hinge formation in deep wide-flange steel beam-columns. Bulletin of Earthquake Engineering 13(4):1097–1118. https://doi.org/10.1007/s10518-014-9640-y
- Elkady, A. and Lignos, D.G. (2018). Full-Scale Testing of Deep Wide-Flange Steel Columns under Multiaxis Cyclic Loading: Loading Sequence, Boundary Effects, and Lateral Stability Bracing Force Demands. Journal of Structural Engineering, 144(2): 04017189. https://ascelibrary.org/doi/pdf/10.1061/(ASCE)ST.1943-541X.0001937
- Suzuki, Y. and Lignos, D.G. (2021). Experimental Evaluation of Steel Columns under Seismic Hazard-Consistent Collapse Loading Protocols. Journal of Structural Engineering, 147(4):04021020. https://ascelibrary.org/doi/full/10.1061/%28ASCE%29ST.1943-541X.0002963
Publications
Related Pages
More projects
MAGNIFY
News
Latest news


PAIRED-HYDRO | Increasing the Lifespan of Hydropower Turbines with Machine Learning
PAIRED-HYDRO | Increasing the Lifespan of Hydropower Turbines with Machine Learning
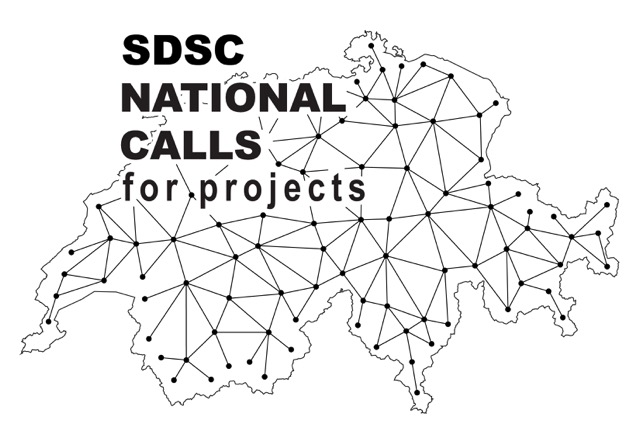
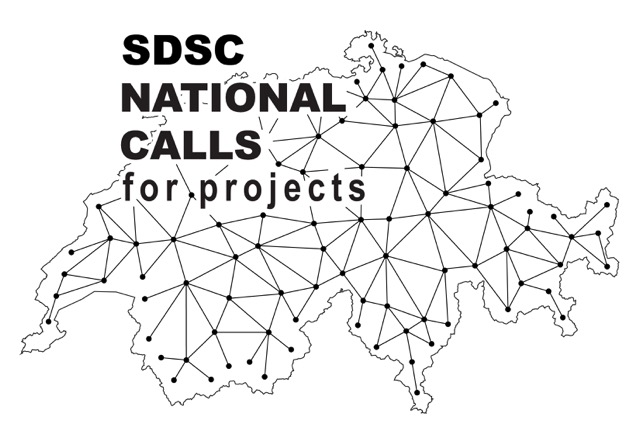
First National Calls: 50 selected projects to start in 2025
First National Calls: 50 selected projects to start in 2025
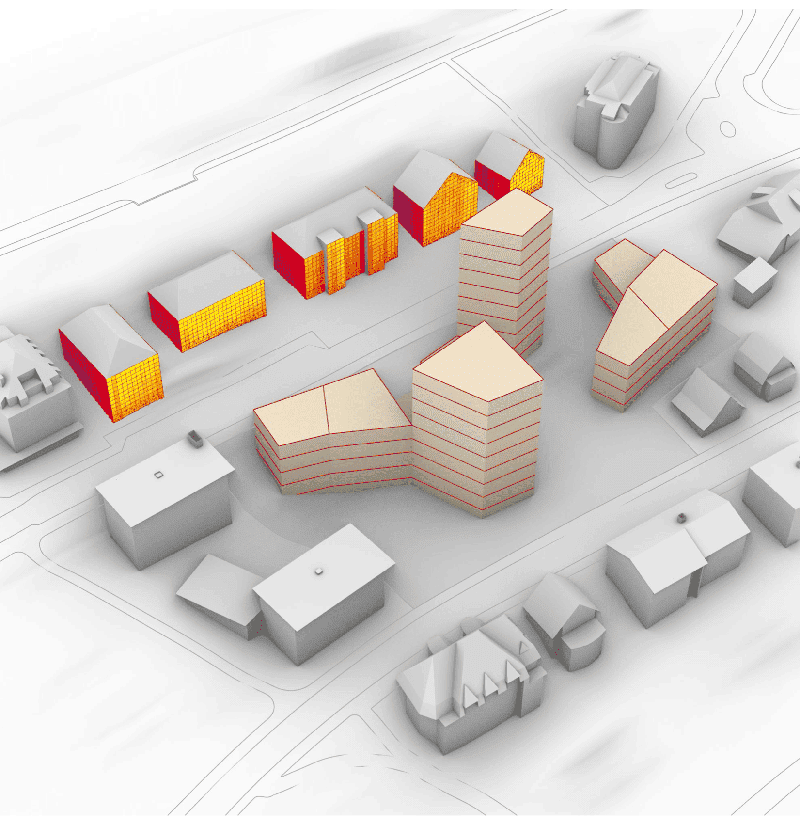
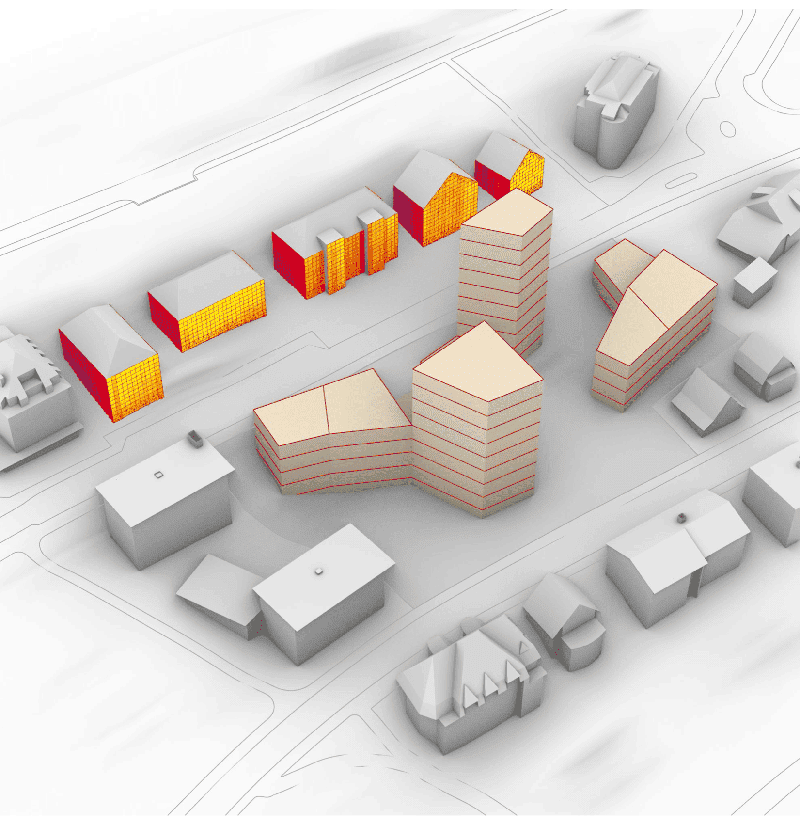
AIXD | Generative AI toolbox for architects and engineers
AIXD | Generative AI toolbox for architects and engineers
Contact us
Let’s talk Data Science
Do you need our services or expertise?
Contact us for your next Data Science project!