Author: Till Muser
PAIRED-HYDRO | Increasing the Lifespan of Hydropower Turbines with Machine Learning
Hydropower accounts for almost 60% of Swiss energy production, which is likely to increase with a shift to renewable energy in the future, with similar trends in the EU. In addition to electricity generation, we will increasingly have to rely upon hydropower to compensate for the fluctuations in production of other renewable energies, like wind and solar, and stabilize the power grid. Adjusting to the grid conditions requires the turbine to transition to a different steady-state point, and such transient operations have become significantly more common since the 2000s.
While any use of the turbine causes fatigue damage, transient operations are considerably more impactful than steady-state operations due to the wide range of dynamic loads experienced by the turbine’s mechanical components. In fact, a single conventional start-up (where the turbine moves from standstill to the best efficiency point (BEP)) can cause as much wear and tear as more than 100 days of steady operation at the BEP!
The PAIRED-HYDRO project aims at identifying the least-damaging start-up trajectory in a data-driven way, using stress measurements as a proxy for fatigue damage [1]. It builds on the results of a previous research project [2] by EPFL-PTMH, which proposed a startup trajectory (alternative to the conventional one) with significantly reduced fatigue damage. Based on the available reduced-scale model tests at EPFL-PTMH, we developed a neural network model for predicting the stress of new control trajectories. Using stress model predictions, we adapted Dijkstra’s algorithm, a classical shortest path finding algorithm, to find the optimal, minimally damaging start-up trajectory, specifying how quickly the turbine has to be accelerated and how quickly the water should be allowed to flow through via the opening of the guide-vanes. The result was then validated on a reduced-scale model with fatigue damage reductions confirmed to be over 99% compared to the classic conventional start-up sequence and over 70% compared to the startup trajectory from [2].
Advanced Test Rig Enables Precise Stress Analysis for Scaled Turbine Models
The EPFL-PTMH laboratory* is equipped with a large, high precision test rig designed specifically for experimental investigation of geometrically scaled turbine models (reduced-scale models) that accurately replicate the behavior of their full-scale counterparts under controlled conditions. This setup allows for detailed performance and efficiency assessment, making it a critical tool for turbine design and operation planning. For this study, stress sensors were installed on the runner blades (which extract energy from the water flow) and the guide vanes (adjustable blades that regulate the incoming water flow). These components are particularly susceptible to fatigue damage. Using this setup, stress data was acquired over multiple start-up control trajectories, allowing evaluation of how different operational strategies influence turbine lifespan.
Understanding Fatigue: How Stress Cycles Shape Component Lifespan
Stress refers to the internal forces within a mechanical component that develop due to external loads. Repeated stress can degrade the material by causing microscopic cracks and tears. These small defects gradually grow with each loading cycle, and once they reach a critical size, the component experiences mechanical failure.
However, this process is inherently stochastic, meaning it is not entirely predictable and depends on various factors such as material properties, manufacturing imperfections, and environmental conditions. Even under identical operating conditions, some components may fail sooner than others due to small, random variations in crack propagation. Additionally, external influences like temperature fluctuations or corrosion can further accelerate or delay the onset of failure. Because of this inherent uncertainty, engineers rely on statistical models and fatigue analysis techniques to estimate the lifespan of mechanical components and design structures that can withstand long-term use.
The stress history of the component can be decomposed into a series of loading cycles (typically using the Rainflow counting method [3]). This series contains the information of what stress differences the component experienced, and how often. Large stress changes can occur as the turbine is accelerated with a motor during start-up but later driven by the water flow. Smaller stress fluctuations occur due to vibration and are of higher frequency. The amount of fatigue damage incurred from a single cycle depends non-linearly on the stress magnitude of the cycle. The cumulative damage is typically computed using a guideline called Miner’s Rule [4], that assumes that the contributions of individual cycles can simply be summed. As a result, both high-magnitude stresses and low stress vibrations contribute to the total fatigue damage.
A time-frequency Neural Network for Stress Modelling
As mentioned in the previous sections, fatigue damage accumulation depends not only on large-amplitude stress variations, which occur during major operational changes like start-up, but also on small, repeated vibrations, which may have smaller amplitudes and higher frequency. Both factors contribute to overall wear and must be considered when assessing the longevity of a turbine.
To produce accurate estimates for the stress, we developed an input Time-Frequency Deep Neural Network (iTF-DNN) model, which is trained to predict both trend and high-frequency oscillations of stress. The trend component of iTF-DNN predicts a low-varying component of the stress based on the current controls via minimization of the mean squared error (MSE) between the predictions and the observed stresses. The high-frequency component is trained in the time-frequency domain to model the residuals between the measured values and the trend. To predict the stress for a new sequence of controls, we sum the trend estimate with the oscillation predictions produced by the second component of our iTF-DNN.
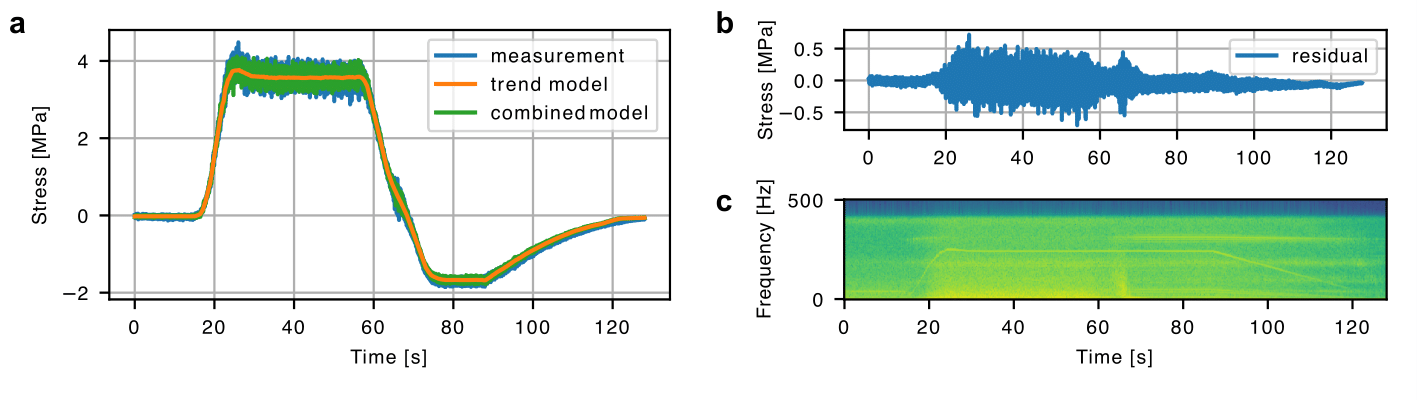
Finding optimal control trajectories for turbine start-up acceleration
A variety of methods exist for optimizing control trajectories, drawing from fields such as variational calculus, control theory, reinforcement learning and graph-based search algorithms. From all approaches considered, we selected Dijkstra’s algorithm [5], a well-established algorithm for solving the shortest-path problem. This algorithm operates on a weighted graph, identifying the most efficient route between a starting node and a goal node. A common analogy is route planning in navigation systems, where the algorithm can determine the shortest path between two cities based on a given road network.
In our application, however, the problem is formulated differently: instead of finding the shortest route between two locations, we seek the optimal control trajectory for transitioning a hydropower turbine from rest (zero rotation and no water flow) to its full operating state (maximum speed and discharge). To achieve this, we discretize the control phase space of turbine speed and discharge, transforming it into a grid. By incorporating constraints on turbine acceleration, we convert this grid into a graph, linking only nodes where transitions are physically feasible. The cost of moving between two nodes is determined by the increase in turbine damage, with damage levels obtained by applying the Rainflow method and Miner's rule to the stress sequence predicted by our neural network stress model. By exploring trajectories in order of increasing damage, the algorithm ensures that the first complete path it finds to the target is the one that minimizes turbine wear.

ML controls to significantly lower damage in physical tests
To validate our results, we conducted reduced-scale model testing to measure the stresses for the control trajectories, comparing three approaches: the conventional classic start-up sequence, a previously designed alternative (non-optimized) trajectory [2], and our newly optimized trajectory.
The experimental measurements confirmed that our optimized trajectory significantly reduces fatigue damage—by over 99.5% compared to the classic start-up and more than 70% compared to the non-optimized alternative (2Slopes). To put this into perspective, a single conventional start-up would cause as much damage as 111 days of continuous operation at maximum speed and discharge. With our optimized trajectory we could significantly lower the damage during start-up to a level equivalent to 9.5 hours of continuous operation (at maximum speed and discharge).
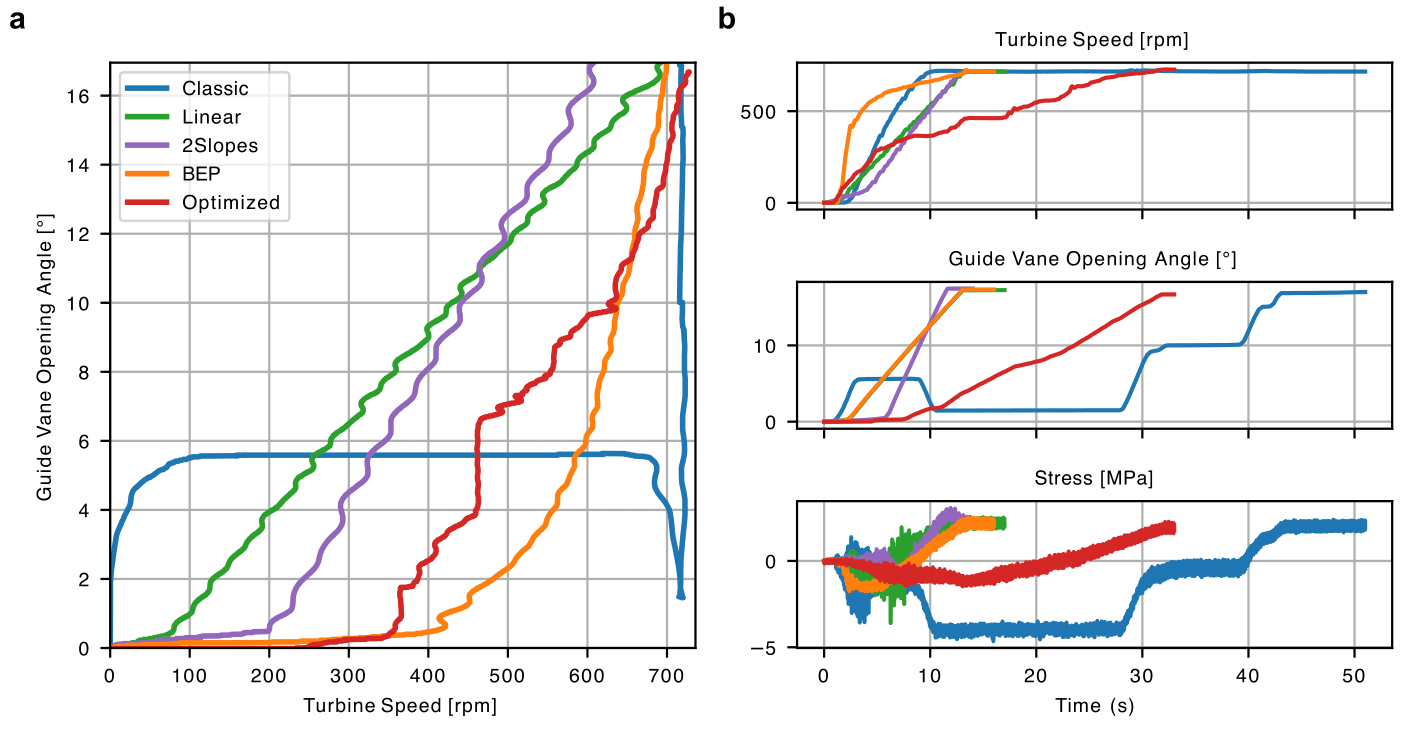
Footnotes
* EPFL PTHM: Technology Platform for Hydraulic Machines Link
References
- Muser, T., Krymova, E., Morabito, A., Seydoux, M., & Vagnoni, E. (2025). Fatigue damage reduction in hydropower startups with machine learning. Nature Communications, 16(1), 2961.
- Seydoux, M., Vagnoni, E., Nicolet, C., Alligné, S., Hugo, N., & Paolone, M. (2022, September). Assessments of hydropower plants start-up sequences and equivalent runner damage under transient operation. In IOP Conference Series: Earth and Environmental Science (Vol. 1079, No. 1, p. 012105). IOP Publishing
- (2017). Practices for Cycle Counting in Fatigue Analysis. ASTM E1049-85, ASTM International. https://doi.org/10.1520/e1049-85r17
- Miner, M. A. (1945). Cumulative Damage in Fatigue. In Journal of Applied Mechanics (Vol. 12, Issue 3, pp. A159–A164). ASME International. https://doi.org/10.1115/1.4009458
- Dijkstra, E. W. (1959). A note on two problems in connexion with graphs. In Numerische Mathematik (Vol. 1, Issue 1, pp. 269–271). Springer Science and Business Media LLC. https://doi.org/10.1007/bf01386390
Image Source
Cover Image: Francis Runner, Grand Coulee Dam; Image Source: Wikipedia.
Displayed figures have been generated in the project.